Siriotek drives technology forward in Marine Energy Conversion
24 January 2020
Unlike Solar and Wind, Marine Energy Conversion (MEC) technology is yet to be established at full commercial level and engineers are racing to devise viable solutions to extract the immense energy within the oceans. When a Renewable Energy Company needed to prove its new tidal MEC concept worked at scale they turned to Siriotek to create bespoke solutions that went from modelling and simulation to successful deployment, reducing the cost of manufacture and upping power efficiency.
The looming energy challenge
With widespread adoption of electric transport and mobility systems global demand for grid power is set to soar in the next 30 years, at a time when most countries are expected to phase out both fossil and nuclear fuel power stations. A major energy unbalance looms on the horizon which must be addressed quickly with innovative, ingenious and sustainable technology.
What feasible options can Renewables offer to replace existing fossil and nuclear capacity while also matching future grid demands? To put the scale of this challenge into context consider that one single nuclear plant provides on average a continuous 1GW of electric power to the grid, which is roughly equivalent to either:
- 950 land based wind turbines (3.5MW each, capacity factor of 30%) taking up a surface of around 10km2 excluding roads, buildings and infrastructures, which is approximately the size of Gibraltar
- 14 millions of solar panels (300W and 0.6m2 each, 25% capacity factor) spread over a comparable amount of land.
Put in other terms, the extent of land required for wind and solar farms to fully replace the fossil and nuclear capacity installed in USA (836GW as of 2017) would be roughly the size of Gambia - which is of course purely theoretical as solar and wind farms make sense only where sun shines, wind blows and communities grant their support, a set of requirements not easily met in power hungry industrialised countries.
These figures suggest that propelling the world into a carbon-free economy on land-based wind and solar alone is wishful thinking, yet the last few years have seen exponential growth of solar and wind farms because technology in these areas has reached commercial level and ROI can be calculated reliably at any scale, which is a major selling point to investors.
By comparison, Marine Energy technology is far less mature and as such represents a significantly riskier and capital intensive proposition: access and deployment of large structures at sea remains expensive and hazardous, which ultimately affects Levelised Cost of Energy (LCOE). However, with oceans covering 71% of the Earth surface and providing a virtually unlimited power resource (usable availability is estimated at 32'000 TWh per year) there is little question that MECs will become an essential part of the energy mix in the near future.
Driven by surging grid demand investments into MECs are rising, opening the way to a milestone shift of balance in Renewables. Developing efficient MECs has become one of the unprecedented technological challenges of our time requiring ingenuity, wisdom, scientific rigour and outstanding problem solving attitude - the same set of skills required to succeed in the competitive realm of Formula 1.
Failure not an option
Several marine based power generation concepts have been devised based on different technologies such as offshore wind, tidal, wave, and ocean thermal energy conversion (OTEC). Very few systems have been developed and demonstrated at full scale in arrays.
Regardless of the technology employed new ventures face enormous market pressure: not only feasibility of each concept must be proven at scale but the substantial development and deployment costs can only be recovered by targeting long operational lifespans of typically 25-30 years. The biggest challenge is therefore
designing durable structures able to produce energy in vast amounts and withstand harsh environment conditions with minimal maintenance in order to achieve a competitive LCOE and minimise CO2 emissions inevitably associated with site-to-shore transport.
The weakest part defines reliability of the entire system: unlike land based systems failure of a minor component in a offshore submarine MEC can involve massive costs for recovery, repair and downtime, potentially compromising long term ROI. This aspect bears a striking similarity to Formula 1, where quest for maximum performance makes details of paramount importance for reliability: failure of a single bolt can make the difference between winning a race or failing to cross the finish line.
Harnessing tidal energy
Established in 2005 as a Renewable venture, Dublin-based OpenHydro patented a unique submarine tidal turbine concept with open centre design for high hydrodynamic efficiency and compatibility with marine wildlife. Openhydro were the first to generate electricity from tidal streams onto the UK National Grid and the first to demonstrate a method of safely deploying and recovering turbines offshore on the seabed.
When they planned to design, build and deploy their largest scale offshore demonstrator they turned to Siriotek for structural engineering and the long term collaboration proved to be a winning match.
Uncharted waters
Unlike wind and solar, submarine tidal streams turbines (TSTs) provide entirely predictable energy flow and do not visually impact landscapes, a key factor for winning community acceptance. In addition, compared to offshore wind farms TSTs do not obstruct navigation of ships and low-flying aircraft, and since water is 830 times denser than air they can be significantly smaller than wind installations of the same power. However TSTs must withstand higher and highly variable structural loading with the addition of possible impact with wildlife and flotsam, corrosive environment and the possibility of blade cavitation at shallower water depths, with ensuing damage.
Openhydro had already successfully designed and tested "small" 6m diameter rotors but plans were now in place to develop and deploy massive 16m turbines to be eventually connected in arrays. Siriotek was asked to come on board as principal consultant for the large scale demonstrator, a monumental engineering challenge with design specifications calling for:
- A larger, 16m diameter and 300t turbine assembly;
- A 700t subsea gravity support structure laid on the seafloor at depths of 50-60m;
- Higher power output (2MW).
With no room for error achieving the operating targets for such a large project required a carefully calculated risk approach. MEC being a nascent industry meant no reliability standards or previous design reference data were available and Openhydro's brilliant engineers had to overcome massive unknowns. So when they looked for a partner to help grind the way to efficient and actionable solutions Siriotek was selected to bring on-board Formula 1 technology and engineering from an industry where delivering effective and practical answers to critical challenges is daily routine.
"Right first time” approach
It was essential to get the design right first time and over the course of the R&D programme Siriotek proposed a number of solutions which were approved for the rotor internal structure, the blade retention system and also the stator support system.
- For each system, Openhydro design team submitted an initial proposal with drawings and CAD data.
- Siriotek would then carry out simulations and structural FEA with sensitivity studies to predict the behaviour of the structures under extreme sea conditions using oceanographic data.
- Durability analysis was employed to drive design improvements whilst reducing weight and simplify manufacturing, with special regard to fabricated parts.
- High-strength corrosion resistant materials and surface treatments from F1 technology were recommended for key stressed components, with specific consideration given to compatibility of metallic interfaces for prevention of galvanic corrosion
- Siriotek would then feed back a number of revised design options with recommended modifications, and after mutual consultations involving cost feasibility, a solution would be selected and the loop start again on the next system.
- In addition to design analysis work Siriotek also devised efficient and cost effective rig testing for specific high risk sub-assemblies to validate results and prove out durability using accelerated test programs
Working together: onsite and remote
To facilitate integration with the design and engineering teams the first month of collaboration was held at the Openhydro design office near the beautiful village of Carlingford, in County Louth. Afterwards design analysis work took place remotely, with regular email contact and video conference reviews to set targets and monitor progress.
Every two weeks, Siriotek delivered a detailed presentation with the outcomes of analyses, simulations, and a number of design variant options with corresponding recommended actions. Video conferencing was used to clear questions or concerns and align the teams before moving on to the next iteration or project phase.
A Technical Success
Siriotek’s simulation processes and design expertise yielded a technical success for the client. We achieved a solution that was structurally efficient but also lightweight, resistant to corrosion, and economically viable for the expected lifespan.
- Problems solved: The most noteworthy structural improvements were achieved with a bespoke design for the turbine stator supports on the subsea base. The solution proposed enhanced durability by 35%, while at the same time delivering a 50% drop in weight and a staggering 60% reduction in weld seam length, with significantly lower fabrication cost compared to the design initially planned.
- USPs achieved: we demonstrated the feasibility of a unique submarine tidal system, able to generate a fully predictable stream of renewable power with no visual impact on the environment.
- Upped durability and reduced manufacturing costs: Siriotek analysis models together with Formula 1 technology and design approach to reliability helped increase overall efficiency and durability whilst reducing weight and manufacturing costs, with direct impact on financial KPIs.
- Outsourced Collaboration: A seamless integration with the remote design team was a key factor for our successful collaboration throughout the 3-years demonstrator programme, resulting in outstanding customer satisfaction.
The project was a technical success, with three demonstrators successfully deployed and operated at sea.
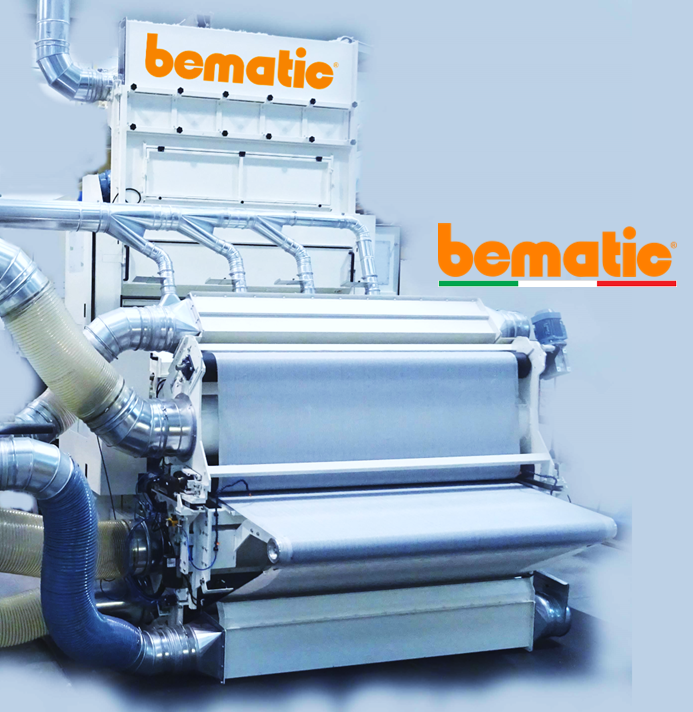
As part of ongoing collaborative efforts focusing on development and optimisation of production technologies for nonwovens, Fraunhofer ITWM and Siriotek have completed feasibility investigations on bematic® latest airlay design “AioLos”. Results are very encouraging and bematic have now committed fully to the new design by confirming manufacturing of a full scale unit, with procurement of parts currently in progress.
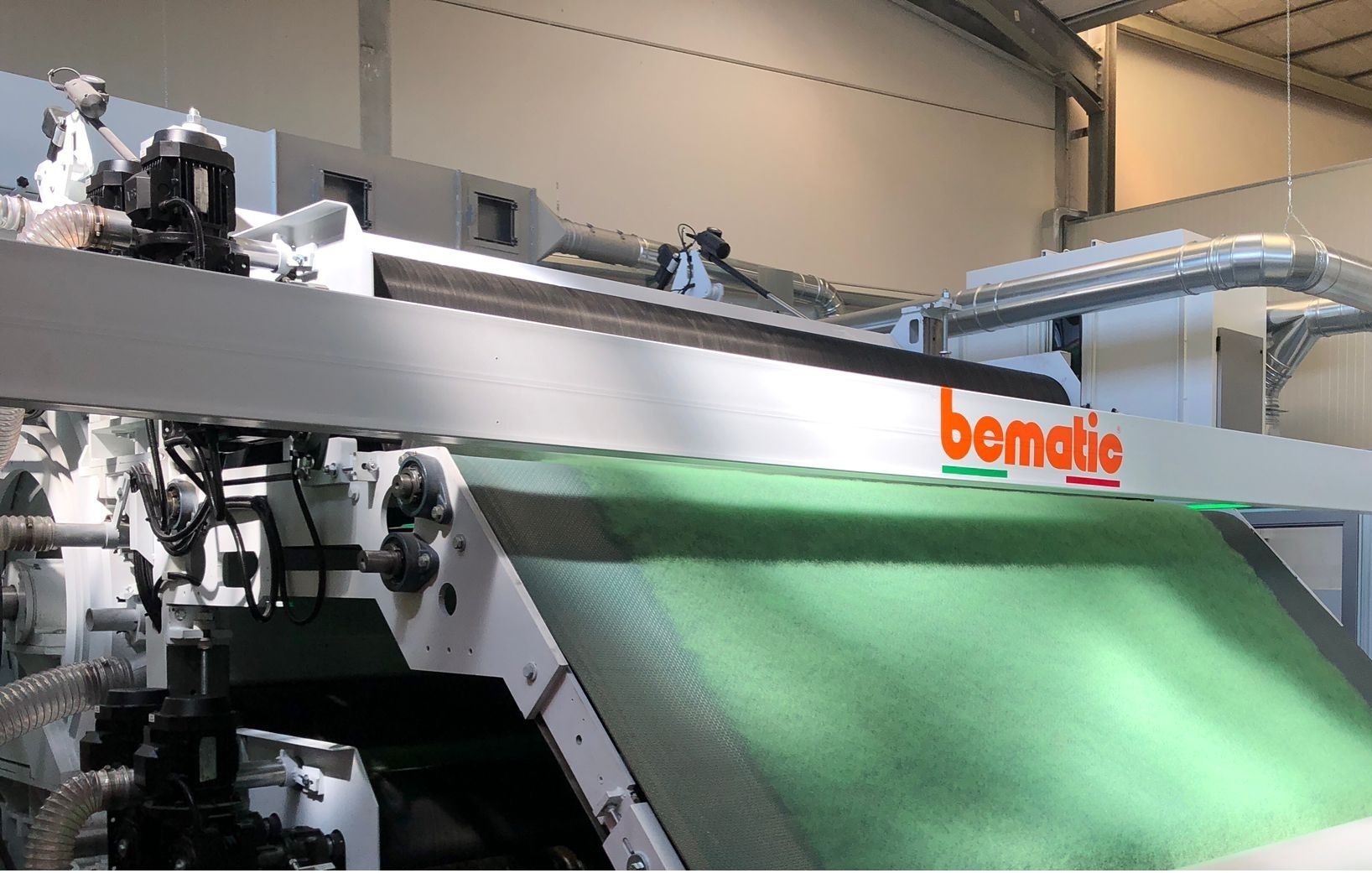
Nonwoven fabrics play today a central role in a number of industries, including automotive, healthcare, medical, construction, and filtration. As demand for these versatile materials continues to grow, Bettarini&Serafini S.r.l (trading as bematic®), Siriotek GmbH and the Fraunhofer Institute for Industrial Mathematics ITWM are now joining forces to enhance and develop air-lay technology for production of nonwovens. The joint project will be presented for the first time at ITMA 2023, the trade fair for textiles technology, materials and innovation.
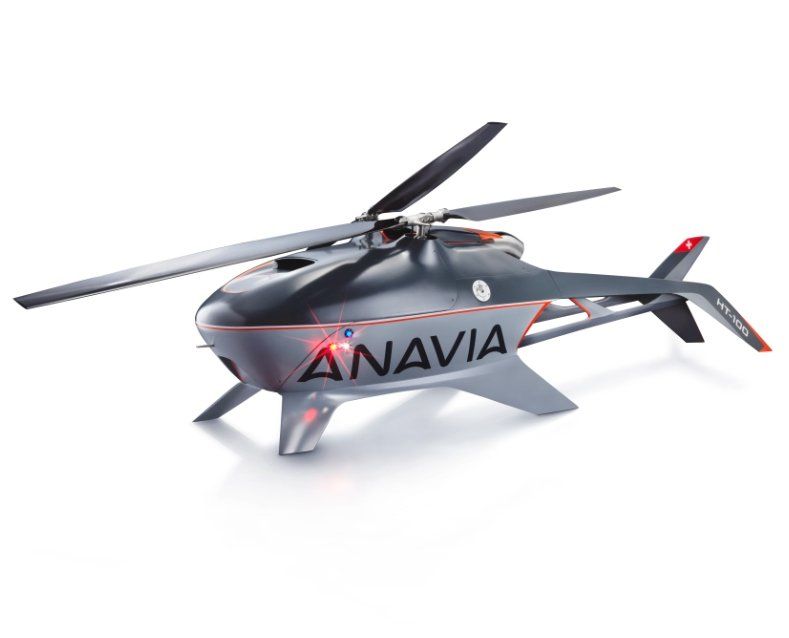
ANAVIA AG, based in Switzerland, is the latest player to join the commercial Unmanned Aerial Vehicles (UAV) market, which is forecasted to grow globally above USD 15bn by 2026 fuelled by widespread adoption across Logistics, Surveillance, Agriculture and Emergency Management. Part of the Connova Group, a global leader in the development of fibre reinforced composites for the Aerospace industry, ANAVIA was established in 2019 with a mission to design, manufacture and commercialise the most advanced UAVs on the market.