Fraunhofer ITWM, Siriotek and bematic® join forces to advance nonwovens production technology
2 June 2023
Nonwoven fabrics play today a central role in a number of industries, including automotive, healthcare, medical, construction, and filtration. As demand for these versatile materials continues to grow, Bettarini&Serafini S.r.l (trading as bematic®), Siriotek GmbH and the Fraunhofer Institute for Industrial Mathematics ITWM are now joining forces to enhance and develop air-lay technology for production of nonwovens. The joint project will be presented for the first time at ITMA 2023, the trade fair for textiles technology, materials and innovation.
Based in Italy,
bematic®
have been developing and manufacturing nonwoven production lines for almost 50 years and today their carding machines are in daily use across the world. The company provides turnkey solutions customised to specific production requirements. bematic® bring to the project their expertise in development and construction of nonwoven production lines and will manufacture the new air-lay systems developed through the joint project.
Swiss-based Siriotek
specialise in mechanical engineering and product development through practical application of virtual prototyping and testing. Throughout the project Siriotek engineers will use analysis, modelling and simulation to drive and optimise the design layout of the new air-lay system.
Fraunhofer ITWM, in turn, contributes to the project with both knowledge and experience in the textile technology and process optimisation, as well as know-how in mathematical modelling and characterization of air-lay processes for staple fibres.
Combining expertise
The three partners aim to jointly develop the next generation of air-lay machines to ensure performance and quality in processing with staple fibres whilst reducing energy consumption, waste generation and carbon emissions. The collaboration brings together the expertise and innovation capabilities of three specialist players in their respective fields.
Faster, denser, more efficient
In air-lay processes raw fibres (natural or synthetic) are opened up and apart by a card roller, introduced into a forced air stream and directed onto conveyor belts. The randomly arranged fibres are then compacted by suction and finally bonded together through mechanical, thermal or chemical processes to achieve web consistency. "Through a collaborative approach, we are pushing the boundaries of air-lay technology to achieve higher production speeds, improved nonwoven uniformity and fibre utilization, and ultimately deliver solutions that are fully tailored to individual production requirements," explains Giovanni Di Lorenzo, Founder and Chief Engineer at Siriotek.
Improved efficiency and sustainability
The project also aims to minimise energy consumption and environmental footprint without compromising performance. “We are driving progress, improving production quality, and contributing to a more sustainable as well as efficient ecosystem in the textile industry” says Dietmar Hietel, Head of the Transport Processes Department at Fraunhofer ITWM.
Giovanni Bettarini, Partner and Commercial director at bematic® adds: “Through this collaboration we will be able to offer more efficient and sustainable manufacturing solutions, tailored to specific applications across automotive, construction, filtration and geotextile”
From June 8 to 14, 2023, the project team will welcome industry representatives to their booth in Hall 10-A101 at ITMA in Milan to share details of the project.
About bematic®
Founded in 1974 in Prato, Italy, Bettarini & Serafini, trading as bematic® have been pioneers in the development of processing lines for nonwovens, with an established reputation for reliability and innovation. Today bematic carding machines operate daily across the globe at leading production companies within diverse industries. bematic® provide highly customised turnkey solutions with a product portfolio covering both traditional carding systems as well as aerodynamic forming lines.
About Siriotek
Based in Zurich, Switzerland, Siriotek provide engineering solutions for product and technology development, with a track record across Aerospace, Formula 1, Renewables, Marine and Robotics. Through a creative approach and significant experience in diverse industries Siriotek engineers specialise in the practical application of virtual modelling, simulation and testing to help innovative companies solve complex problems and efficiently develop new products and technologies.
About the Fraunhofer Institute for Industrial Mathematics ITWM
The Fraunhofer Institute for Industrial Mathematics ITWM in Kaiserslautern is one of the largest research institutes for applied mathematics worldwide. We see our task in further developing mathematics as a key technology and in providing innovative impulses. Our focus is on the implementation of mathematical methods and technology in application projects and their further development in research projects. The close interaction with partners from industry guarantees the high practical relevance of our work.
Its integral components are consulting, implementation and support in the application of high-performance computing technology and the provision of customized software solutions. Our various competencies address a wide range of customers: automotive industry, mechanical engineering, chemical industry, energy and finance. This also benefits from our good networking, for example in the Simulation and Software-based Innovation Performance Center.
About the Fraunhofer Society
The Fraunhofer-Society, based in Germany, is the world's leading organization for application-oriented research. With its focus on key technologies of relevance to the future and on the exploitation of the results in business and industry, it plays a central role in the innovation process. As a guide and stimulus for innovative developments and scientific excellence, it helps shape our society and our future. Founded in 1949, the organization currently operates 76 institutes and research facilities in Germany. More than 30,000 employees, most of them trained in the natural sciences or engineering, produce the annual research volume of 2.9 billion euros. Of this, 2.5 billion euros is spent on contract research
Press contacts
bematic® – Bettarini & Serafini Srl
Via Schio 59100
Prato PO Italy
Siriotek GmbH
Technoparkstrasse 1
8005 Zurich Switzerland
FRAUNHOFER ITWM
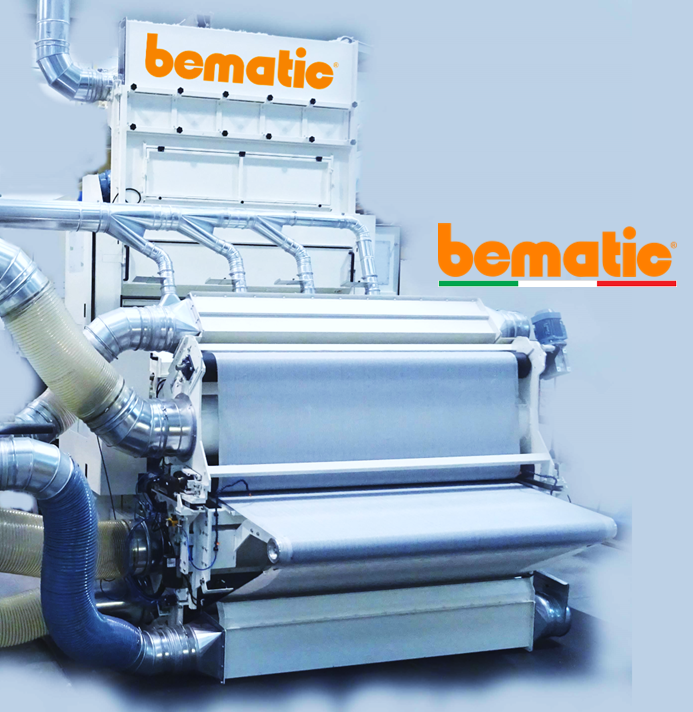
As part of ongoing collaborative efforts focusing on development and optimisation of production technologies for nonwovens, Fraunhofer ITWM and Siriotek have completed feasibility investigations on bematic® latest airlay design “AioLos”. Results are very encouraging and bematic have now committed fully to the new design by confirming manufacturing of a full scale unit, with procurement of parts currently in progress.
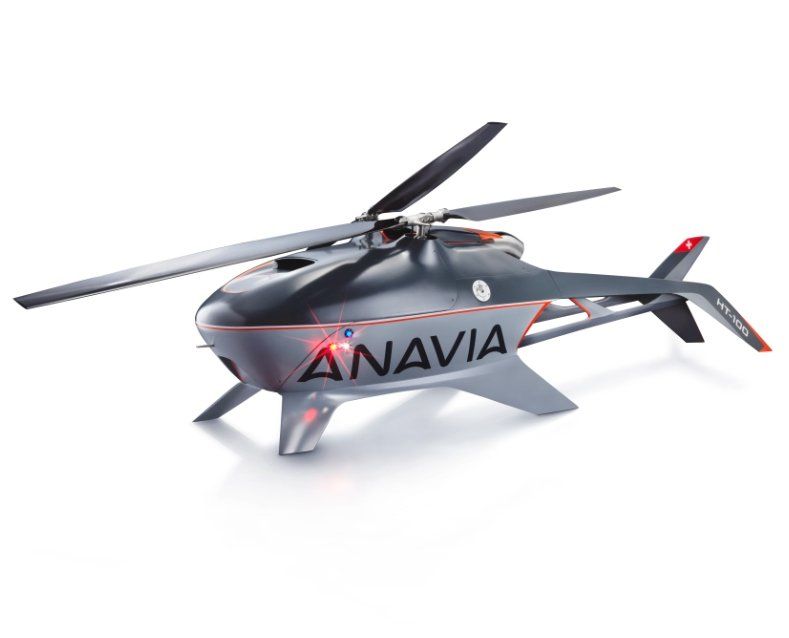
ANAVIA AG, based in Switzerland, is the latest player to join the commercial Unmanned Aerial Vehicles (UAV) market, which is forecasted to grow globally above USD 15bn by 2026 fuelled by widespread adoption across Logistics, Surveillance, Agriculture and Emergency Management. Part of the Connova Group, a global leader in the development of fibre reinforced composites for the Aerospace industry, ANAVIA was established in 2019 with a mission to design, manufacture and commercialise the most advanced UAVs on the market.